Make this article seo compatible,Let there be subheadings for the article, be in french, create at least 700 wordsDüsseldorf Lorsque vous atteignez le village de Waldenbuch dans le district de Böblingen, l’odeur du chocolat remplit vos narines. Le fabricant de chocolat Ritter Sport emploie ici 1 000 de ses 1 900 employés dans le monde, dont environ la moitié dans la production de chocolat. Ils travaillent en trois équipes, les machines fonctionnent 24 heures sur 24 et peuvent produire plus de trois millions de barres par jour.Mais la délicate fonte du chocolat a une empreinte CO2 amère. Cela est dû au fait que le cacao nécessaire à cela provient du Nicaragua ou du Ghana ou de la Côte d’Ivoire. Selon les calculs de l’Institut de recherche sur l’énergie et l’environnement de Heidelberg pour le compte de l’Agence fédérale de l’environnement, une barre de 100 grammes génère en moyenne 410 grammes de CO2. Là – et pas seulement là – il y a un potentiel d’économies.L’important, selon l’entreprise familiale fondée en 1912, est d’économiser de l’énergie à chaque étape de la production de chocolat. Chez Ritter Sport, le thème de la durabilité a commencé avec la catastrophe du réacteur en Ukraine en 1986. Après la catastrophe de Tchernobyl, l’actionnaire majoritaire Alfred Ritter ne trouvait plus de noisettes non traitées, s’est appuyé sur ses propres plantations et a repensé. L’entreprise cultive désormais également son propre cacao au Nicaragua.La production en Allemagne est climatiquement neutre depuis 2019, « depuis 2020, nous pouvons nous appeler une entreprise climatiquement neutre selon le GHG Protocol », explique Asmus Wolff, responsable de la chaîne d’approvisionnement et de l’énergie au sein du conseil d’administration . Les émissions non réductibles sont compensées par des certificats Gold Standard. La prochaine étape devrait être la neutralité climatique totale, qui sera élaborée avec les fournisseurs de matières premières tout au long de la chaîne d’approvisionnement. Dernier objectif de décarbonation en date : 42 % de réduction des émissions d’ici 2030 selon l’initiative Science Based Targets, qui a validé les objectifs de l’entreprise. L’objectif : des économies d’énergie de 1,5 % par an par rapport à l’année précédente. La première étape pour y parvenir : les mesures.Le suivi de la production aurait dû être la norme depuis longtemps – mais ce n’est pas le cas »Des milliers de points de mesure sont réunis dans nos usines », explique Asmus Wolff. Les données des points de mesure seraient rassemblées dans des systèmes centraux. « Alors, l’intelligence artificielle sera désormais également utilisée en plus de la nôtre », déclare Wolff. Aujourd’hui, vous pouvez immédiatement savoir où l’énergie est gaspillée. Des capteurs sont utilisés pour mesurer en continu les vibrations, la génération de chaleur et les niveaux de bruit dans les systèmes, par exemple. Cela permet de prédire où les problèmes pourraient survenir à l’avenir. De cette façon, on peut « intervenir de manière proactive » avant que le gaspillage ne se produise. Chez Ritter Sport, il y a aussi une petite équipe dans le cadre de la gestion de l’énergie et des bâtiments dont la tâche est d’identifier les voleurs d’énergie. L’équipe enregistre de nouveaux succès chaque semaine, dit Wolff.Dietmar Gründig dirige le département Industrie, mobilité et efficacité énergétique de l’Agence allemande de l’énergie Dena. Il dit: Un effort de mesure comme celui de Ritter Sport devrait être la norme dans les entreprises – mais dans de nombreux cas, ce n’est pas encore le cas. Au moins, cependant, nous sommes sur la bonne voie : l’expert affirme que les systèmes de mesure numériques exploitent déjà un potentiel considérable d’efficacité. Et cela « à l’aide de nombreuses petites mesures, parfois avec de faibles investissements ».Chez Ritter Sport, comme dans de nombreuses sociétés de production, les usines ont été construites au fil des décennies : il y a des machines qui ont été achetées en 1950, explique Asmus Wolff, mais il y a aussi des machines des années 2020. Avec la technologie moderne, mais aussi avec un nouveau savoir-faire, l’entreprise peut agir sur la base de la mesure. « Aujourd’hui, nous comprenons encore mieux comment faire du chocolat à la perfection », explique le responsable. « Par exemple, comment optimiser les paramètres d’agitation sans remettre en cause les exigences de qualité internes. » Asmus Wolff Dans la direction du fabricant de chocolat, le manager est responsable des chaînes d’approvisionnement et des questions énergétiques. (Photo : Johannes Wosilat/Ritter Sport) Concrètement, cela signifie qu’il existe un rythme de brassage optimal pour chacune des machines très différentes dans les différentes parties de la production. Afin d’atteindre le même niveau de qualité partout, vous devez définir des intervalles d’agitation très différents en fonction des résultats de mesure.76 % de puissance en moins lors de l’agitationC’est ce qu’ils ont fait chez Ritter Sport – et cela en valait la peine. Environ 140 conteneurs ont pu être optimisés de cette manière, chaque machine dispose désormais des intervalles d’agitation optimaux pour les masses de chocolat et de fourrage. Résultat : 76 % d’électricité en moins sont désormais nécessaires pour l’agitation. Cela correspond à plus de 900 000 kilowattheures par an. Le facteur décisif ici est l’effort avec lequel la masse brute est chauffée.Lorsque la pâte de cacao et le beurre arrivent dans les usines, les matières premières sont d’abord mélangées avec du sucre et, si nécessaire, de la poudre de lait. Les rouleaux assurent que leur consistance devient plus fine. Pour ce faire, les machines du fabricant de chocolat ont d’abord besoin d’une température de 50 degrés.Lorsque le chocolat passe par le processus de production, il doit être relativement liquide, ce qui nécessite à nouveau de la chaleur. Le chocolat prend son onctuosité dans les conques, c’est-à-dire des machines qui bougent et remuent en même temps. Cela nécessite une température de travail de 60 degrés. Enfin, pour amener le chocolat dans sa forme finale, il doit être refroidi – dans le cas des chocolats fourrés, ce refroidissement doit être répété une fois de plus avant que le fourrage ne soit mis en place. Le défi : utiliser le moins d’énergie possible pour l’agitation, le chauffage et le refroidissement dans tous ces processus. Chez Ritter Sport, l’énergie elle-même provient de sources régénératives. Depuis 2002, nous produisons exclusivement de l’électricité verte. Il y a des systèmes photovoltaïques sur le toit de l’entrepôt, et il y a 15 ans, un système combiné de chaleur et d’électricité a été installé, ce qui vous permet de générer de l’énergie et de la chaleur en même temps. L’entreprise dispose également d’une centrale de production combinée de chaleur et d’électricité. Il devrait être supprimé d’ici 2025. La chaleur et l’électricité seront alors fournies par plusieurs pompes à chaleur, qui à leur tour seront alimentées en électricité par les propres centrales solaires et éoliennes de l’entreprise. Une partie de l’énergie électrique pourrait alors produire 3,5 parties de chaleur ou de froid, de sorte que la demande énergétique totale de production diminuerait considérablement. C’est un énorme avantage de la technologie des pompes à chaleur, déclare Asmus Wolff.La flotte de camions est devenue électriqueMais la plus grande source de perte d’énergie chez Ritter Sport est l’air comprimé. Il est conduit à travers toute l’usine via d’innombrables tuyaux. « Il y a des pertes par frottement ou fuites », explique Wolff. « Contrairement à l’eau, vous ne le voyez pas. » La plupart des entreprises ont « un thème » ici. L’air comprimé est un levier important, explique Dietmar Gründig de Dena : les mesures sur l’air comprimé sont très efficaces car c’est une source d’énergie précieuse et coûteuse.Série : Voici comment l’Allemagne sauveEn plus d’économiser de l’énergie dans la production, Ritter Sport a converti au début de l’année sa propre flotte de camions pour le transport de marchandises entre les usines et les entrepôts en véhicules électriques. « Cela nous permet d’économiser jusqu’à 500 tonnes de CO2 », déclare Asmus Wolff.Avec toutes les mesures, il est surprenant que l’empreinte carbone de l’entreprise familiale ait augmenté de 2021 à 2022. Selon Wolff, la raison en est que depuis 2022, le lait en poudre a été évalué plus haut qu’auparavant lors de la mesure de l’empreinte CO2. Cela modifie les bilans sans que l’entreprise ait émis plus de CO2, explique Wolff. « Pour moi, la chose la plus importante est ce que nous avons vraiment amélioré dans la réalité. »Plus: Comment Ago Energie a révolutionné l’industrie des pompes à chaleur industrielles – et économise ainsi de l’électricité
Source link -57
Customize this title in frenchOù le fabricant de chocolat Ritter Sport économise de l’énergie
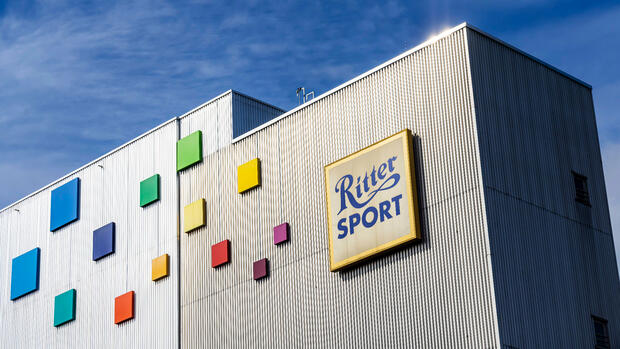