Make this article seo compatible,Let there be subheadings for the article, be in french, create at least 700 words Le nouveau processus de fabrication produit des pièces de véhicules en aluminium à haute résistance qui réduisent les coûts et sont plus respectueuses de l’environnement. RICHLAND, Washington — Les rebuts d’aluminium peuvent désormais être collectés et transformés directement en nouvelles pièces de véhicules grâce à un procédé innovant développé par l’industrie automobile, en particulier pour les véhicules électriques. [This month], le laboratoire national du nord-ouest du Pacifique du ministère de l’Énergie, en collaboration avec la société de technologie de mobilité leader Magna, dévoile un nouveau procédé de fabrication qui réduit plus de 50 % de l’énergie grise et plus de 90 % des émissions de dioxyde de carbone en éliminant le besoin d’exploiter et raffiner la même quantité de minerai d’aluminium brut. L’aluminium léger peut également aider à étendre l’autonomie des véhicules électriques. Ce procédé breveté et primé de traitement et d’extrusion assistés par cisaillement (ShAPE™) collecte les rebuts et les restes de garnitures en aluminium de la fabrication automobile et les transforme directement en matériau approprié pour les nouvelles pièces de véhicules. Il est maintenant mis à l’échelle pour fabriquer des pièces en aluminium légères pour les véhicules électriques. L’avancée la plus récente, décrite en détail dans un nouveau rapport et dans un article de recherche de Manufacturing Letters, élimine le besoin d’ajouter de l’aluminium nouvellement extrait au matériau avant de l’utiliser pour de nouvelles pièces. En réduisant le coût du recyclage de l’aluminium, les fabricants peuvent être en mesure de réduire le coût global des composants en aluminium, leur permettant ainsi de mieux remplacer l’acier. « Nous avons montré que les pièces en aluminium formées avec le procédé ShAPE répondent aux normes de l’industrie automobile en matière de résistance et d’absorption d’énergie », a déclaré Scott Whalen, scientifique des matériaux au PNNL et chercheur principal. « La clé est que le procédé ShAPE décompose les impuretés métalliques dans la ferraille sans nécessiter une étape de traitement thermique énergivore. Cela seul permet de gagner un temps considérable et introduit de nouvelles efficacités. Le nouveau rapport et les publications de recherche marquent l’aboutissement d’un partenariat de quatre ans avec Magna, le plus grand fabricant de pièces automobiles en Amérique du Nord. Magna a reçu un financement pour la recherche collaborative du Bureau des technologies des véhicules du DOE, Programme du Consortium des matériaux légers (LightMAT). « La durabilité est au premier plan de tout ce que nous faisons chez Magna », a déclaré Massimo DiCiano, responsable de la science des matériaux chez Magna. « De nos processus de fabrication aux matériaux que nous utilisons, et le processus ShAPE est une excellente preuve de la façon dont nous cherchons à évoluer et à créer de nouvelles solutions durables pour nos clients. » La microstructure d’un trapèze en aluminium présente une taille de grain très raffinée et uniforme, essentielle pour obtenir un produit solide et fiable.(Image reproduite avec l’aimable autorisation de Nicole Overman ; mise en valeur par Cortland Johnson | Pacific Northwest National Laboratory) Avantages de l’aluminium Outre l’acier, l’aluminium est le matériau le plus utilisé dans l’industrie automobile. Les propriétés avantageuses de l’aluminium en font un composant automobile attractif. Plus léger et résistant, l’aluminium est un matériau clé dans la stratégie visant à fabriquer des véhicules légers pour une meilleure efficacité, qu’il s’agisse d’étendre l’autonomie d’un véhicule électrique ou de réduire la taille de la capacité de la batterie. Bien que l’industrie automobile recycle actuellement la majeure partie de son aluminium, elle y ajoute régulièrement de l’aluminium primaire nouvellement extrait avant de le réutiliser, pour diluer les impuretés. Les fabricants de métaux s’appuient également sur un procédé centenaire de préchauffage des briques, ou « billettes », comme on les appelle dans l’industrie, à des températures supérieures à 1 000 °F (550 °C) pendant de nombreuses heures. L’étape de préchauffage dissout les amas d’impuretés telles que le silicium, le magnésium ou le fer dans le métal brut et les distribue uniformément dans la billette grâce à un processus appelé homogénéisation. En revanche, le procédé ShAPE accomplit la même étape d’homogénéisation en moins d’une seconde puis transforme l’aluminium solide en un produit fini en quelques minutes sans étape de préchauffage nécessaire. « Avec nos partenaires de Magna, nous avons atteint une étape critique dans l’évolution du processus ShAPE », a déclaré Whalen. « Nous avons démontré sa polyvalence en créant des pièces carrées, trapézoïdales et multicellulaires qui répondent toutes à des critères de qualité en matière de résistance et de ductilité. Extrusions fabriquées à partir de déchets industriels AA6063 par ShAPE produisant des profils (a) circulaires, (b) carrés, (c) trapézoïdaux et (d) trapézoïdaux à deux cellules. (Image reproduite avec l’aimable autorisation de Scott Whalen | Laboratoire national du nord-ouest du Pacifique) Pour ces expériences, l’équipe de recherche a travaillé avec un alliage d’aluminium appelé 6063, ou aluminium architectural. Cet alliage est utilisé pour divers composants automobiles, tels que les berceaux de moteur, les ensembles de pare-chocs, les longerons de châssis et les garnitures extérieures. L’équipe de recherche du PNNL a examiné les formes extrudées à l’aide de la microscopie électronique à balayage et de la diffraction par rétrodiffusion d’électrons, ce qui crée une image du placement et de la microstructure de chaque particule métallique dans le produit fini. Les résultats ont montré que les produits ShAPE sont uniformément résistants et dépourvus de défauts de fabrication qui pourraient entraîner la défaillance des pièces. En particulier, les produits ne présentaient aucun signe de grands amas de métaux, des impuretés qui peuvent entraîner une détérioration des matériaux et qui ont entravé les efforts visant à utiliser de l’aluminium recyclé secondaire pour fabriquer de nouveaux produits. L’équipe de recherche examine actuellement des alliages d’aluminium encore plus résistants généralement utilisés dans les boîtiers de batterie des véhicules électriques. « Cette innovation n’est que la première étape vers la création d’une économie circulaire pour l’aluminium recyclé dans la fabrication », a déclaré Whalen. « Nous travaillons actuellement sur l’inclusion des flux de déchets post-consommation, ce qui pourrait créer un tout nouveau marché pour les déchets d’aluminium secondaires. » En plus de Whalen, l’équipe de recherche du PNNL comprenait Nicole Overman, Brandon Scott Taysom, Md. Reza-E-Rabby, Mark Bowden et Timothy Skszek. En plus de DiCiano, les contributeurs de Magna comprenaient Vanni Garbin, Michael Miranda, Thomas Richter, Cangji Shi et Jay Mellis. Ce travail a été soutenu par le bureau des technologies des véhicules du DOE, programme LightMAT. La technologie brevetée ShAPE est disponible sous licence pour d’autres applications. Par Karyn Hede, PNNL. Avec l’aimable autorisation du Laboratoire national du nord-ouest du Pacifique. Inscrivez-vous pour recevoir les mises à jour quotidiennes de CleanTechnica par e-mail. Ou suivez-nous sur Google Actualités !
Vous avez un conseil pour CleanTechnica, souhaitez faire de la publicité ou suggérer un invité pour notre podcast CleanTech Talk ? Contactez-nous ici. Solar PV & Farming — Tendances en agrovoltaïque Je n’aime pas les paywalls. Vous n’aimez pas les paywalls. Qui aime les paywalls ? Chez CleanTechnica, nous avons mis en place un paywall limité pendant un certain temps, mais cela nous a toujours semblé faux – et il a toujours été difficile de décider ce que nous devrions y mettre. En théorie, votre contenu le plus exclusif et le meilleur passe derrière un paywall. Mais alors moins de gens le lisent ! Nous n’aimons tout simplement pas les paywalls, et nous avons donc décidé d’abandonner les nôtres. Malheureusement, le secteur des médias est encore une entreprise difficile et acharnée avec de minuscules marges. C’est un défi olympique sans fin de rester au-dessus de l’eau ou peut-être même… haleter – grandir. Donc … Si vous aimez ce que nous faisons et que vous souhaitez nous soutenir, veuillez contribuer un peu chaque mois via PayPal ou Patreon pour aider notre équipe à faire ce que nous faisons ! Merci! Publicité
!function(f,b,e,v,n,t,s) if(f.fbq)return;n=f.fbq=function()n.callMethod? n.callMethod.apply(n,arguments):n.queue.push(arguments); if(!f._fbq)f._fbq=n;n.push=n;n.loaded=!0;n.version=’2.0′; n.queue=[];t=b.createElement(e);t.async=!0; t.src=v;s=b.getElementsByTagName(e)[0]; s.parentNode.insertBefore(t,s)(window, document,’script’, ‘https://connect.facebook.net/en_US/fbevents.js’); fbq(‘init’, ‘1020645035249848’); fbq(‘track’, ‘PageView’); !function(f,b,e,v,n,t,s) if(f.fbq)return;n=f.fbq=function()n.callMethod? n.callMethod.apply(n,arguments):n.queue.push(arguments); if(!f._fbq)f._fbq=n;n.push=n;n.loaded=!0;n.version=’2.0′; n.queue=[];t=b.createElement(e);t.async=!0; t.src=v;s=b.getElementsByTagName(e)[0]; s.parentNode.insertBefore(t,s)(window,document,’script’, ‘https://connect.facebook.net/en_US/fbevents.js’); fbq(‘init’, ‘438121713776676’); fbq(‘track’, ‘PageView’);
Source link -57
Customize this title in frenchL’aluminium recyclé offre des économies d’énergie, d’émissions et d’autonomie de batterie de véhicule électrique
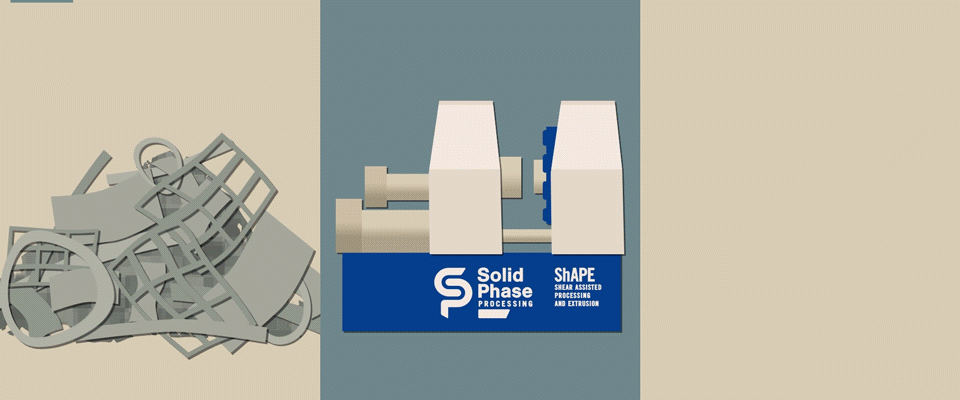