Make this article seo compatible,Let there be subheadings for the article, be in french, create at least 700 words Nous l’avons dit de nombreuses fois, de plusieurs façons. La technologie de la batterie n’est pas une chose statique. Des centaines d’entreprises et de laboratoires à travers le monde, y compris le laboratoire national d’Oak Ridge, recherchent la prochaine technologie de batterie qui conduira à des voitures électriques moins chères avec une autonomie plus longue et une charge plus rapide. À cet égard, Volkswagen affirme avoir mis au point un nouveau procédé de revêtement à sec qui lui permettra de faire baisser le prix de ses voitures électriques de plusieurs centaines de dollars. Selon Le Spiegel (paywall), Volkswagen a l’intention de mettre en production à grande échelle un nouveau procédé de revêtement à sec pour les batteries de voitures électriques. Le revêtement sec réduit de 30 % la consommation d’énergie dans la production des cellules de batterie, ce qui pourrait faire baisser le coût des voitures électriques de plusieurs centaines d’euros par véhicule. Volkswagen termine la phase de test de la batterie Sebastian Wolf, membre du conseil d’administration de la filiale de batteries Volkswagen PowerCo, a récemment déclaré que la méthode de revêtement à sec des électrodes s’était avérée viable lors de tests internes, ce qui a conduit PowerCo à investir davantage dans le processus et à installer une ligne pilote dans un laboratoire près de Salzgitter, en Allemagne. . La première usine de batteries de PowerCo sera située à Salzgitter, dans le cadre d’un plan du groupe Volkswagen visant à rendre sa chaîne d’approvisionnement de véhicules électriques plus intégrée verticalement, en particulier lorsqu’il s’agit de fabriquer les batteries qui alimenteront ses voitures électriques à l’avenir. VW construit également une grande usine de batteries au Canada. Selon Wolf, Volkswagen étudie le nouveau procédé de revêtement à sec avec des partenaires depuis 2020 et prévoit de l’utiliser dans la production de millions de cellules de batterie d’ici le début de 2027. À ce jour, l’entreprise a investi environ 40 millions d’euros dans la recherche la technologie de revêtement à sec. Un certain nombre d’entreprises et d’instituts de recherche dans le monde travaillent déjà sur des procédés de revêtement à sec pour les électrodes. Une batterie lithium-ion conventionnelle fabriquée aujourd’hui est généralement constituée d’une feuille métallique recouverte d’un revêtement mince qui contient les composants actifs qui permettent le stockage de l’énergie. Le processus de revêtement est généralement effectué avec une pâte semi-liquide produite à partir de matériaux actifs qui comprennent des noirs conducteurs et des liants avec un solvant. La pâte est ensuite étalée sous forme de couche humide sur la feuille de métal – généralement du cuivre. D’énormes lignes de production avec de très longues distances de séchage sont nécessaires pour que le solvant s’évapore ensuite. Le processus de revêtement à sec rendrait toutes ces étapes superflues, ce qui réduirait considérablement l’espace nécessaire à la fabrication des batteries et l’énergie nécessaire au processus de séchage. Parmi les acteurs très actifs dans ce domaine figure une alliance de Siemens, LiCAP Technologies et BW Papersystems. Il y a environ six mois, le trio a formé un partenariat stratégique pour fabriquer et commercialiser de tels équipements pour l’industrie des cellules de batterie. Tesla travaille également sur un revêtement sec pour ses grandes cellules 4680. Plus récemment, il a été signalé que Tesla pouvait enduire à sec l’anode, mais était toujours aux prises avec des problèmes de revêtement sec sur la cathode. Volkswagen, 24M et QuantumScape Volkswagen pense à l’avenir en ce qui concerne les futurs systèmes de production. En 2021, l’entreprise a investi dans la startup américaine de batteries 24M Technologies, qui va encore plus loin que le procédé de revêtement à sec avec un procédé semi-solide. Volkswagen est licencié depuis 2021. À cette époque, il a déclaré: «À l’avenir, une optimisation significative des coûts de production de batteries sera obtenue en réduisant l’utilisation de matériaux et en éliminant plusieurs étapes du processus de production conventionnel. À cette fin, une nouvelle filiale de Volkswagen poursuivra le développement et la mise à l’échelle de la technologie sur la base des droits de brevet de 24M pour les applications automobiles. Volkswagen avait également investi dans QuantumScape, une autre société basée aux États-Unis qui promet de mettre sur le marché des batteries à semi-conducteurs. QuantumScape et 24M Technologies visent la fin de cette décennie avant que leurs batteries ne soient prêtes pour la production commerciale. Selon Le Spiegelle nouveau procédé de revêtement à sec pourrait également ne pas voir la production commerciale avant la fin de cette décennie. D’une manière ou d’une autre, les batteries qui alimenteront les véhicules électriques en 2030 sont encore aujourd’hui au laboratoire. Volkswagen pense voir une opportunité ici, mais il est impossible de savoir quelles autres percées technologiques de la batterie pourraient se produire en cours de route. L’avenir est tellement imprévisible ! Percée de l’ORNL à semi-conducteurs Plus tôt dans cet article, nous avons fait référence à de nouvelles recherches des laboratoires nationaux d’Oak Ridge concernant les batteries à semi-conducteurs. Dans un article de recherche publié récemment dans la revue Lettres énergétiques ACS, des chercheurs dirigés par Marm Dixit et ses collègues de l’ORNL ont découvert que le pressage isostatique peut créer de fines couches d’électrolyte solide et uniforme, en maintenant un niveau élevé de contact entre les couches pour un mouvement ionique fluide. Le procédé fonctionne avec une variété de compositions de batterie à différentes températures et pressions. Avec l’aimable autorisation de l’ORNL Ce processus utilise des fluides et des gaz comme l’eau, l’huile et l’argon à l’intérieur d’une machine pour appliquer une pression constante sur un composant de la batterie, créant ainsi un matériau hautement uniforme. Avec l’aide d’un partenaire industriel qui produit cet équipement de pressage, les chercheurs de l’ORNL ont découvert que le pressage isostatique pouvait faciliter et accélérer la production de batteries tout en créant de meilleures conditions pour le flux d’énergie. Parmi les résultats prometteurs, le pressage isostatique s’est avéré extrêmement efficace à basse température et avec des matériaux électrolytiques mous, qui sont plus faciles à traiter et qui ont des structures cristallines favorables au mouvement des ions. Auparavant, le pressage isostatique des batteries était effectué principalement à des températures très élevées ou à température ambiante, mais pas entre les deux. « Tous ces matériaux ont leurs avantages uniques que les chercheurs aimeraient exploiter », a déclaré Dixit. « C’est pourquoi il est important que vous puissiez effectuer un pressage isostatique à n’importe quelle température ambiante à plusieurs milliers de degrés Fahrenheit : cela signifie que vous pouvez utiliser n’importe quoi, des polymères aux oxydes, en passant par toute la gamme de matériaux. » Cette polyvalence est la clé d’un processus de fabrication cohérent pour la grande variété de conceptions de batteries à semi-conducteurs et de matériaux en cours de développement, a déclaré Dixit. Le pressage isostatique serait également relativement facile à développer commercialement – une découverte qui a suscité une attention considérable alors que les entreprises se précipitent pour fournir des batteries à semi-conducteurs aux constructeurs automobiles. Plusieurs grands constructeurs automobiles ont annoncé leur intention de vendre des véhicules électriques fonctionnant avec des batteries à semi-conducteurs d’ici quelques années. Ilias Belharouak, membre d’entreprise à l’ORNL et chef de sa section d’électrification, a déclaré que la technologie des batteries à semi-conducteurs doit être perfectionnée pour la fabrication à grande échelle. « Ne vous y trompez pas, toutes les batteries à semi-conducteurs sont sur le long terme », a-t-il déclaré. « Mais la technologie de pressage isostatique, si elle est évolutive, fournirait un moyen d’assembler les couches de batterie sans pressions externes peu pratiques. » Le pressage isostatique est utilisé depuis des décennies dans les matériaux de collage et d’assemblage par fusion. Récemment, il a été un outil pour éliminer les vides et les anomalies dans les pièces imprimées en 3D. Cependant, ses tests pour les applications de batterie ont été limités. Les chercheurs de l’ORNL ont indiqué que le pressage isostatique pourrait également permettre de fabriquer les trois couches de batterie en un seul système dense plutôt que de les créer séparément avant de les assembler. Dans le Lettres énergétiques ACS papier, l’équipe de Dixit a souligné l’importance de poursuivre une batterie à semi-conducteurs qui peut être mise à l’échelle pour la fabrication. « Relever efficacement ce défi ferait passer la technologie actuelle des batteries au cours des prochaines décennies en permettant aux batteries à semi-conducteurs à haute densité énergétique de répondre aux demandes croissantes de…
Source link -57
Customize this title in frenchVolkswagen affirme que le nouveau processus de batterie sèche permettra d’économiser des centaines de dollars par voiture
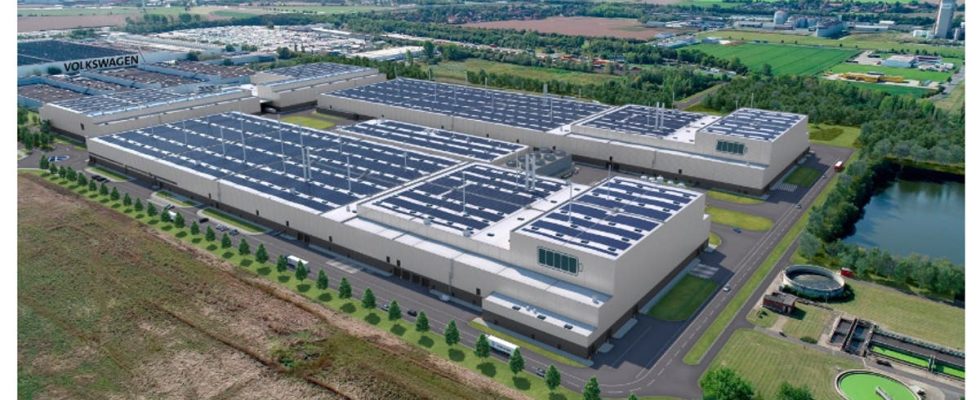