Make this article seo compatible,Let there be subheadings for the article, be in french, create at least 700 words Derrière les plaques signalétiques fantaisistes des voitures que nous achetons – Mercedes, BMW, Audi, etc. – se cache toute une industrie qui fournit les pièces et composants qui font de ces voitures ce qu’elles sont. Des sièges aux radios en passant par les écrans tactiles, les pare-brise et les pneus, les fournisseurs apportent les composants nécessaires à la fabrication d’automobiles directement sur les quais de chargement des usines automobiles du monde entier. Les meilleurs d’entre eux sont connus collectivement sous le nom de fournisseurs de niveau 1, et au sein de ce groupe, l’allemand ZF est l’un des meilleurs parmi les meilleurs, avec d’autres sociétés de premier plan telles que Bosch, Magna International et Siemens. ZF compte 165 000 employés dans le monde et exploite 168 sites de production dans 32 pays. Au cours de l’exercice 2022, ZF a réalisé un chiffre d’affaires de 43,8 milliards d’euros. Sur sa page d’accueil, elle se décrit comme une entreprise technologique mondiale fournissant des systèmes pour les voitures particulières, les véhicules utilitaires et la technologie industrielle, permettant la prochaine génération de mobilité. ZF permet aux véhicules de voir, de penser et d’agir. Dans les quatre domaines technologiques du contrôle du mouvement des véhicules, de la sécurité intégrée, de la conduite automatisée et de la mobilité électrique, ZF propose des solutions complètes de produits et de logiciels pour les constructeurs automobiles établis. L’entreprise utilise une Porsche Taycan qu’elle appelle EVbeat comme banc d’essai pour une suite de nouveaux produits pour les voitures électriques. En ce qui concerne l’avancement de la cause de la mobilité électrique, ZR a annoncé le 29 juin une nouvelle unité d’entraînement intégrée pour les voitures électriques qui pèse moins et a un couple plus élevé que n’importe lequel de ses concurrents. « La mobilité durable est au cœur de notre stratégie d’entreprise », a expliqué Stephan von Schuckmann, membre du conseil d’administration de ZF responsable des systèmes de transmission électrifiés. « Sur la base d’un véhicule de production extrêmement efficace, nous montrons le potentiel qu’offrent les futurs composants d’entraînement électrique lorsque nous les combinons dans un système global encore plus efficace. » La société affirme que son EVSys800 est une unité d’entraînement modulaire de 800 volts qui intègre une électronique de puissance en carbure de silicium avec le moteur électrique et un réducteur. Comparé à son unité d’entraînement actuelle de 800 volts, l’EVSys800 est plus léger de 40 kilogrammes (88 lb), ce qui peut entraîner un groupe motopropulseur beaucoup plus léger. Moins de poids sous le capot signifie plus de capacité pour les personnes et les choses à l’intérieur. L’unité a une puissance nominale continue de 206 kW avec un pic de 275 kW. Le couple maximal serait de 70 Newton-mètres par kilogramme de poids. À 74 kilogrammes, cela signifie que l’EVSys800 a plus de 5000 Newton-mètres de couple disponibles sur l’essieu moteur. Le nouveau boîtier est 50 mm plus étroit que l’unité actuelle, grâce à un réducteur plus compact et à la technologie « Braided Winding » brevetée par ZF utilisée pour fabriquer le moteur électrique. Une telle unité d’entraînement à haute puissance est capable de générer beaucoup de chaleur pendant le fonctionnement à pleine puissance. Pour résoudre ce problème, ZF fait circuler l’huile de refroidissement directement autour des tiges de cuivre à l’intérieur du moteur, là où la majeure partie de la chaleur est générée. Le système de refroidissement très efficace augmente considérablement les performances sans augmenter la taille ou le poids de l’unité d’entraînement. La nouvelle unité élimine également le besoin de matériaux de terres rares afin que le moteur électrique puisse être fabriqué de manière plus durable. La technologie « Braided Winding » développée et brevetée par ZF est un développement ultérieur de ce que l’on appelle le bobinage ondulé et permet une réduction de 10 % de l’espace nécessaire à l’intérieur du carter du moteur. Il réduit également la quantité de cuivre nécessaire d’environ 10 %. L’onduleur de l’entraînement électrique a été entièrement repensé, tout comme tous les autres composants essentiels. Un nouveau réducteur coaxial transmet les efforts d’entraînement du moteur électrique via deux trains épicycloïdaux. Ils génèrent non seulement le rapport de démultiplication final souhaité, mais assurent également la fonction différentielle entièrement intégrée. Par rapport aux concepts de décalage conventionnels, dans lesquels les arbres d’entrée et de sortie ne sont pas sur le même axe, la solution coaxiale réduit le poids et les exigences d’espace d’installation sans compromettre l’efficacité, le bruit et les vibrations. En combinaison avec la technologie Braided Winding, ce lecteur peut être considérablement plus court, permettant une installation dans presque tous les espaces d’installation de véhicules. « Notre objectif était de rendre cette transmission aussi compacte et légère que possible tout en maintenant une dynamique de conduite élevée et en augmentant l’efficacité en fonctionnement réel », a déclaré le Dr Otmar Scharrer, responsable du développement des systèmes de transmission électrique chez ZF. « En termes de densité de couple, nous sommes en haut du podium lorsque nous nous comparons aux e-drives pour voitures particulières actuellement disponibles sur le marché. Dans le même temps, nous avons accordé une grande attention à l’aspect durabilité lors du développement. Avec ce système, nous pouvons parfaitement répondre aux principales exigences de nos clients, à savoir l’efficacité, les performances et les coûts. Les premières unités de production de la nouvelle chaîne cinématique ZF seront disponibles à partir de 2026. Système de chauffage et de refroidissement révisé Le chauffage et la climatisation peuvent drainer beaucoup d’énergie des batteries des voitures électriques. Non seulement l’habitacle doit rester à une température confortable, mais la batterie doit également être refroidie pendant la charge à haute puissance ou chauffée par temps froid. En plus de sa nouvelle unité de puissance EVSys800, ZF a également développé un système de chauffage et de refroidissement intégré à commande numérique appelé TherMaS qui est suffisamment léger et compact pour s’adapter à la plupart des véhicules d’aujourd’hui. Le cœur du système est une pompe à chaleur de 800 volts qui utilise du propane comme réfrigérant. Il peut sembler contre-intuitif d’utiliser un combustible fossile dans une voiture électrique, mais les pompes à chaleur au propane sont parmi les plus efficaces disponibles aujourd’hui. L’efficacité est la priorité numéro un des véhicules électriques pour parcourir de longues distances sans recharger. Selon ZF, le système TherMaS peut augmenter l’autonomie d’un véhicule électrique jusqu’à un tiers par temps froid. Le concept TherMaS comporte trois circuits désignés. Au centre se trouve le très petit circuit de réfrigérant qui est pré-rempli et hermétiquement fermé pour le rendre sans entretien. De plus, le concept n’a pas d’interface avec d’autres zones du véhicule, telles que l’intérieur. ZF utilise le propane réfrigérant naturel sans fluor. Le nouveau système utilise deux fois moins de réfrigérant qu’une pompe à chaleur conventionnelle, tout en fournissant deux fois plus de puissance de refroidissement. Le système est conçu pour répondre à la fois aux températures relativement élevées du moteur électrique et réguler la température de l’électronique de puissance et de charge. Le logiciel de contrôle régule la capacité de refroidissement. Systèmes de contrôle électronique et cloud ZF a développé son propre logiciel de groupe motopropulseur qui met en réseau tous les systèmes du véhicule et établit la connexion au cloud ZF. La société affirme que son nouveau progiciel peut anticiper les températures de fonctionnement optimales pour toute voiture électrique en fonction des profils de conduite ou des conducteurs individuels, et préparer le système en conséquence. Par exemple, la climatisation et le refroidissement du système sont réduits lorsque de courtes distances sont détectées. Le système d’assistance électronique peut également donner des conseils directs aux conducteurs sur la façon d’utiliser efficacement le véhicule électrique. Par exemple, une accélération et une décélération efficaces ainsi qu’une vitesse maximale optimisée sont affichées, ce qui est particulièrement précieux lorsqu’il s’agit de calculer une autonomie précise et pratique avant le début d’un trajet. Les plats à emporter ZF ne construit pas de voitures, il fabrique les composants qui permettent aux constructeurs automobiles de produire de meilleures voitures – et des caravanes. Aujourd’hui, de nombreuses entreprises préfèrent intégrer leurs chaînes d’approvisionnement en interne. Tesla, par exemple, n’achète pas de sièges à un fournisseur. Il les fabrique lui-même selon ses propres spécifications. Et pourtant, un fournisseur extérieur comme ZF peut être en mesure d’utiliser des économies d’échelle pour rendre les composants disponibles à un coût inférieur…
Source link -57
Customize this title in frenchZF dévoile un système d’entraînement compact à couple élevé pour les voitures électriques
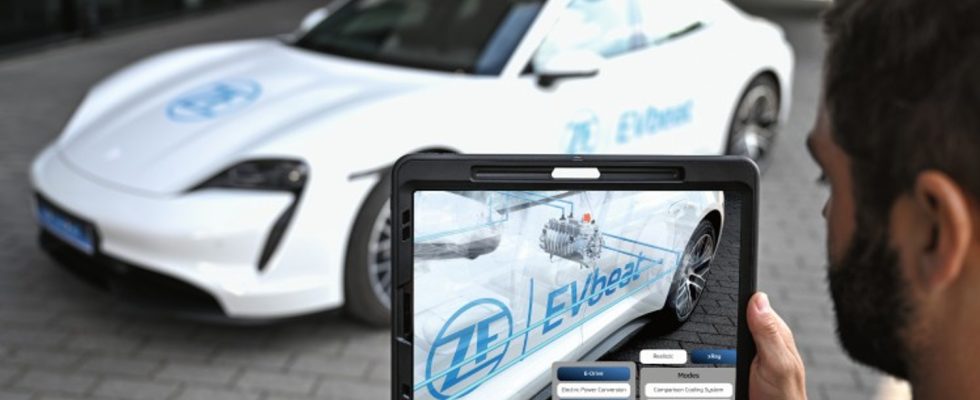